A module from the Subaru Prime Focus Spectrograph (PFS) at Caltech Astronomy is supported by a Flotron 202 benchtop Rotation Fixture during assembly, integration and test operations. Each module consists of (quantity 57) Ø7.7mm x 10 cm long fiber positioning robots, nicknamed “Cobra”. Each robot supports an optical fiber and functions to drive the fiber to its commanded position within a patrol region of approximately Ø9.5mm. Establishing a patrol region for each fiber eliminates the potential for tangling of the fibers. Each fiber (approximately 65 meters in length) is a conduit of light collected at the focal plane and delivered to the spectrographs located in a room next to the telescope. The finished spectrograph system will incorporate 42 of these modules (laid out in a hexagonal shape) and contain 2,394 fiber positioners capable of simultaneous observation of up to 2,394 targets at one time, a technology breakthrough.
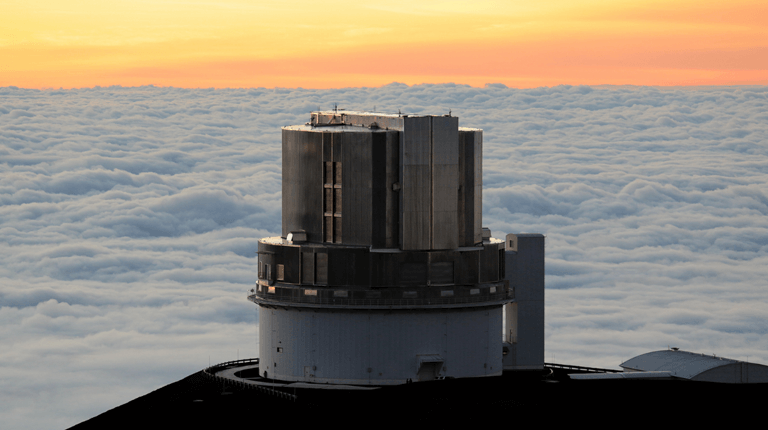
Flotron’s 202 Benchtop Rotation Fixture has a 130 lbs load rating considering SFy = 2 and SFu = 3. Trunnion lock knobs on the end frame bearing housings eliminate backlash in the system. Additionally, a 15° index plate can be physically pinned to the vertical upright to lockout the rotation axis. Standard interfaces include either mounting plates or angle mounts. The standard finish option is compatible in a CLASS 10K clean room environment. The end frames are powder coated Flotron blue and the gearbox is wet painted Flotron blue. All of the moving parts and hardware are zinc plated. An ESD ground lug can be utilized for compatibility in electro-statically protected areas. Learn more about Flotron’s 200 Series Benchtop Rotation Fixture product line.
